Industrial excellence at the service of healthcare
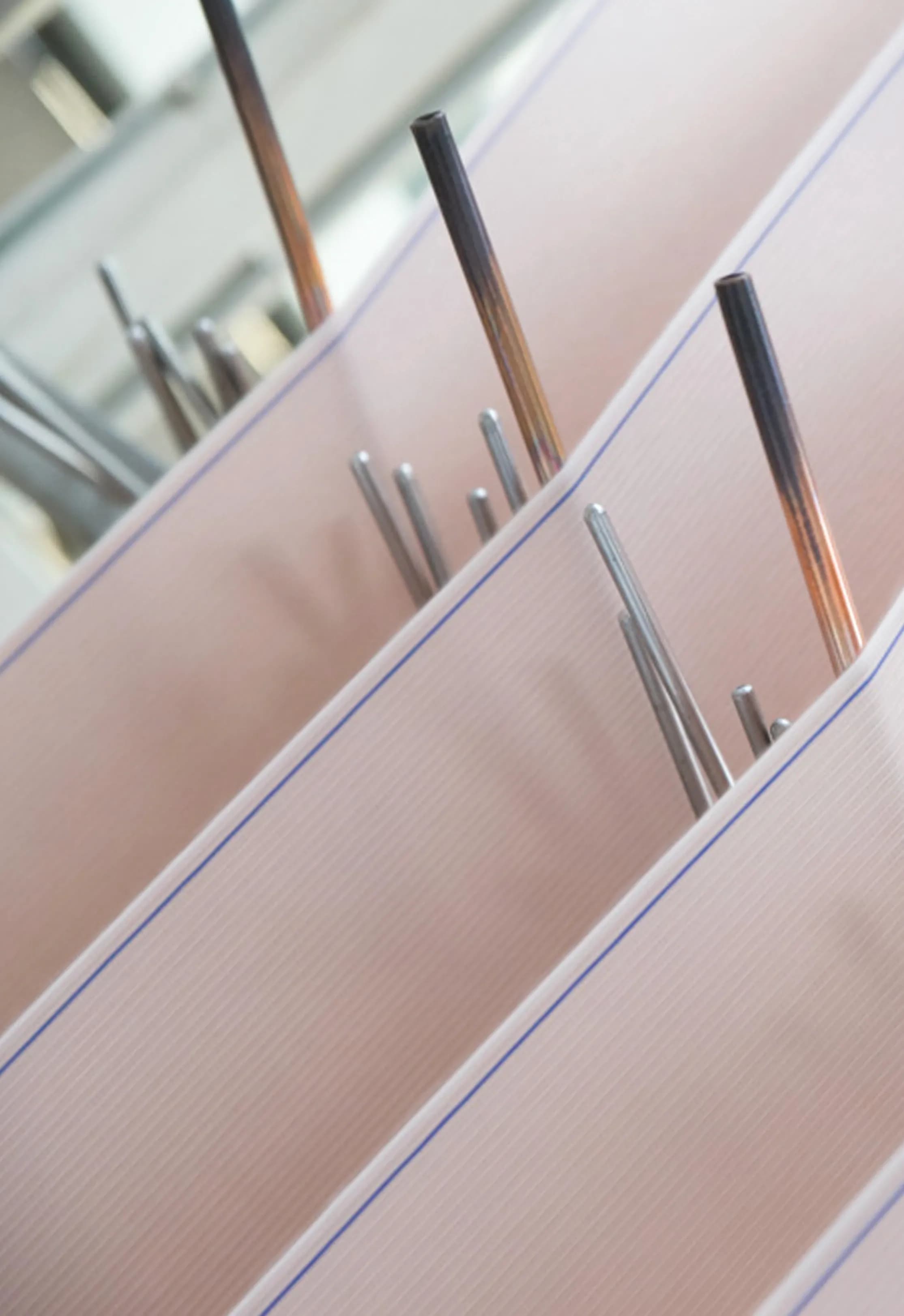
An industrial model for quality and efficiency
Thuasne® controls its entire value chain, from the selection of raw materials to the distribution of the finished product. With 16 production sites and 3 logistics centers around the world, the Group creates and supplies medical devices tailored to the needs of patients and healthcare professionals.
This integrated industrial model allows us to offer products designed, manufactured and distributed using technologies mastered in-house and based on long-standing experience: a true signature of "made in Thuasne®".
Thuasne®'s strength also lies in its ability to mass-produce medical devices to patient specifications. The result is custom solutions to support compliance.
This flexible industrial approach ensures high standards of quality, efficiency and innovation.
Thuasne®'s industry
16
production sites in Europe, North America and Africa
8
million products shipped annually
5,300
kilometers of technical fabrics produced annually in France
21
million kilometers of knitted yarn
Excellence in textile craftsmanship
With more than 175 years' experience, Thuasne® is a key player in the medical and sports textiles sector. Thanks to its in-depth mastery of manufacturing processes, the Group designs medical devices that combine quality, comfort and performance. This textile expertise is used to create braces and compression solutions.
From yarn to finished product, Thuasne® integrates the major processing stages.
Covering
Wrapping the elastic yarns with one or more covering yarns to improve strength, guarantee durability and comfort of use.
Flat and circular knitting
Interlacing one or more yarns to produce a knitted fabric.
Weaving
Interlacing yarns to produce a fabric.
Dyeing
Apply a color to the fiber.
Assembly
Cutting, welding and making the product.
Finishing
Giving the fabric its final appearance and achieving the defined characteristics.
Post-Forming
Stabilizing and drying the product by heat treatment.
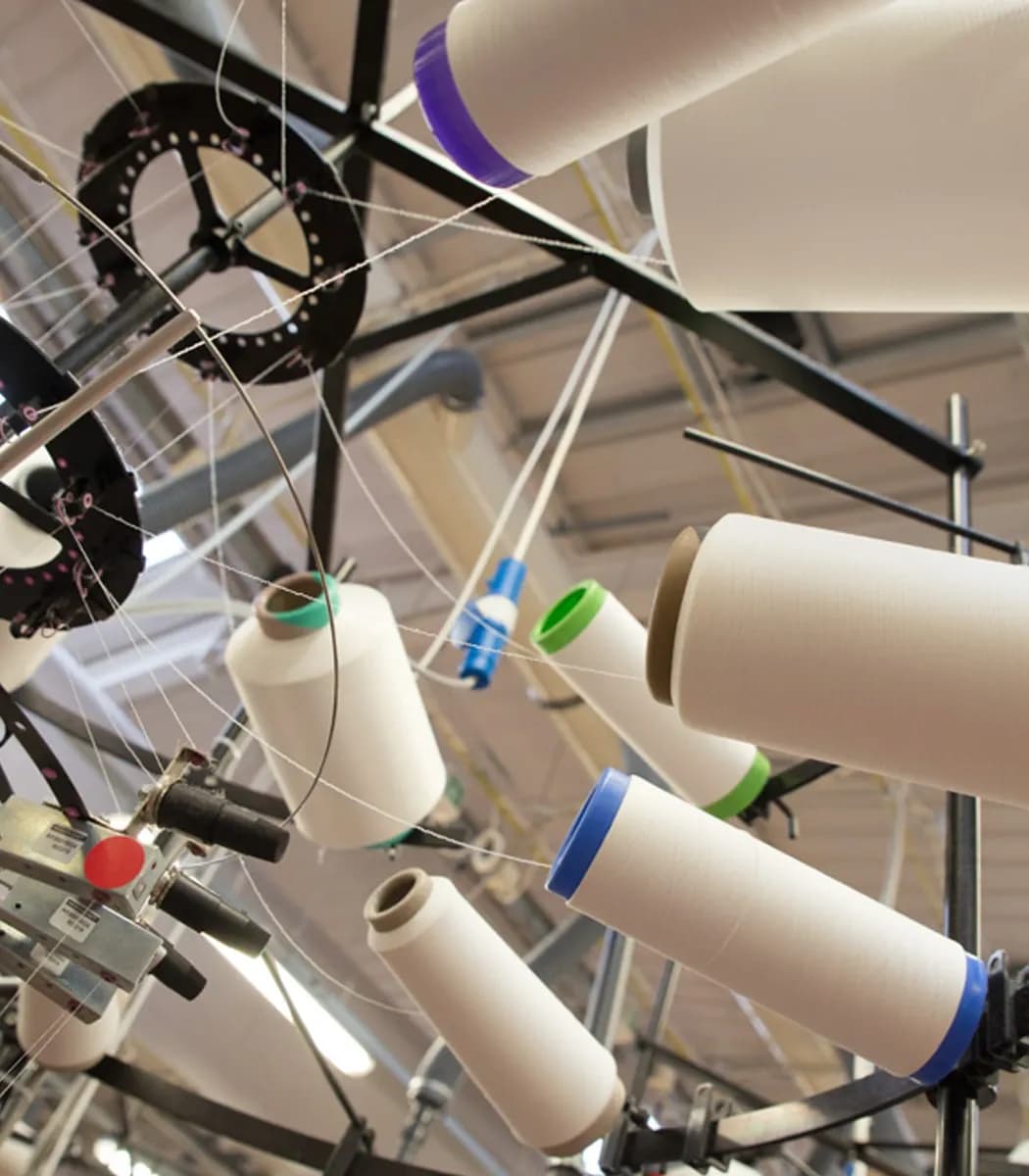
Mastering materials in all their forms
Thuasne® know-how also relies on the use of materials adapted to the clinical specificities and use of each product.
To achieve this, the Group uses a wide range of materials, from natural fibers (wool, cotton, linen) to man-made fibers (viscose) and synthetics (polyamide, polyester, elastane).
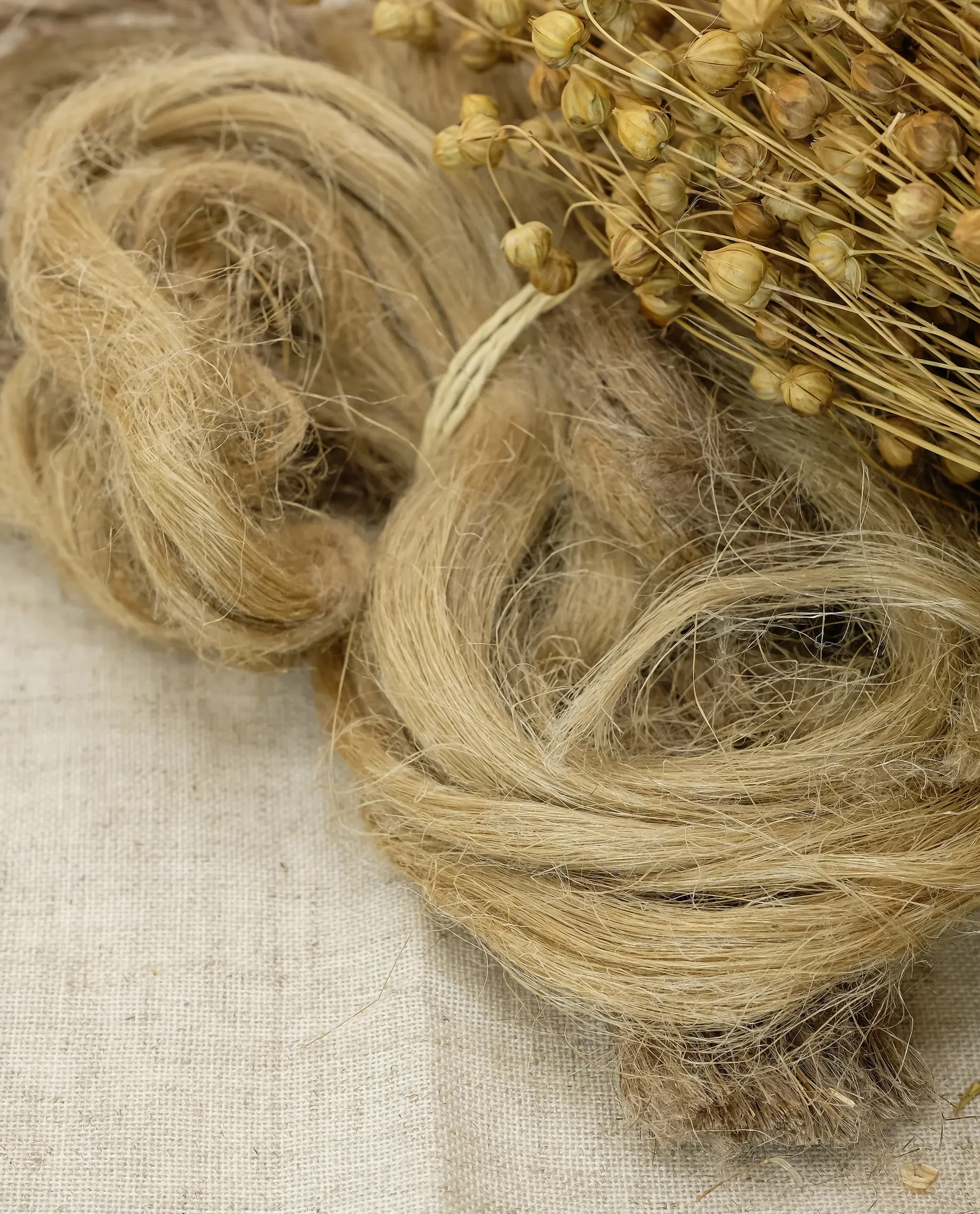
Innovative materials at the heart of our solutions
At Thuasne®, innovation is not limited to textiles. The Group has an extremely comprehensive range of materials at its disposal, enabling it to design cutting-edge solutions for patients. Lightweight, strong, flexible... these materials possess unique properties, enabling us to produce excellent quality solutions for patients worldwide.
Metals
Metals are very strong and durable materials. To manufacture its solutions, Thuasne® uses aluminum recognized for its lightness and steel with high tensile and compression resistance.
Composites
Composite materials consist of fibers embedded in a matrix, usually resin. This combines the lightness of fibers with the strength of the matrix. Carbon fiber has high tensile strength, while glass fiber offers excellent shock absorption.
Silicone
This synthetic polymer has great flexibility and outstanding thermal stability. A wide range of hardnesses is available to suit the needs of each solution.
Thermoplastics
These plastics can be melted and reformed several times without significantly altering their properties.
Combining technical expertise and innovation, Thuasne® stands out for its mastery and ingenious use of a variety of materials. The Group is now investing in artificial intelligence and motorization technologies to develop intelligent orthotics.